Les délais de livraison qui s’allongent et les ruptures de stock chez certains fournisseurs font partie des mauvaises surprises qui ont causé bien des soucis à la plupart des entreprises depuis le début de la pandémie. Aux prises avec ces problèmes, Lumen fait partie des entreprises qui tentent de s’adapter.
« Notre modèle, c’est de livrer le lendemain partout au Québec, explique le président du distributeur de matériel électrique, Serge Leblanc, en entrevue téléphonique. Donc, quand je n’ai pas le matériel, mes clients sont mal servis. »
L’entreprise qui appartient au Groupe Sonepar, établi en France, a ainsi décidé qu’il lui fallait davantage d’espace pour de l’emmagasinage.
En croissance, Lumen, qui se spécialise notamment dans la coupe de câble, prévoyait déjà ajouter entre 80 000 et 100 000 pi2 de superficie à ses installations inaugurées en 2016 en bordure de l’autoroute 440, à Laval. Les perturbations de la chaîne d’approvisionnement ont toutefois incité M. Leblanc et son équipe à aller plus loin.
« Avec tout ce que l’on a vécu, nous […] avons décidé d’y aller avec 180 000 pi2 pour nous donner une capacité de stockage encore plus grande », affirme-t-il.
Mise au point au Japon dans les années 1950 et déployée dans l’industrie automobile, l’approche du juste-à-temps a été perfectionnée et s’est élargie à la quasi-totalité des secteurs au fil du temps. Elle consiste à coordonner la production en fonction des commandes. On achète la quantité de matériel nécessaire à chaque étape du processus.
Les producteurs reçoivent les marchandises au fur et à mesure, ce qui leur permet d’éviter de consacrer du temps et de l’argent à l’entreposage des stocks.
« C’est un modèle efficace, mais on essayait d’étirer l’élastique au maximum pour minimiser les stocks », explique Simon Stien, directeur de pratique chez GCL Group, qui se spécialise dans les conseils en matière de chaîne d’approvisionnement et de logistique. « Aujourd’hui, il est difficile de rattraper tout cela. »
Les grands constructeurs automobiles en sont un bon exemple. Frappés de plein fouet par la pénurie de semi-conducteurs – composants que l’on trouve dans des puces électroniques essentielles au fonctionnement de certains modules –, plusieurs ont été contraints d’interrompre temporairement leur production.
Des traces dans les livres
L’emmagasinage de composants – lorsqu’ils sont disponibles – est l’une des façons d’atténuer les mauvaises surprises dans le contexte actuel. Mais une augmentation des stocks se reflète sur le bilan financier d’une entreprise.
M. Leblanc dit avoir fait un « choix » pour placer ses clients « au centre de ses décisions ».
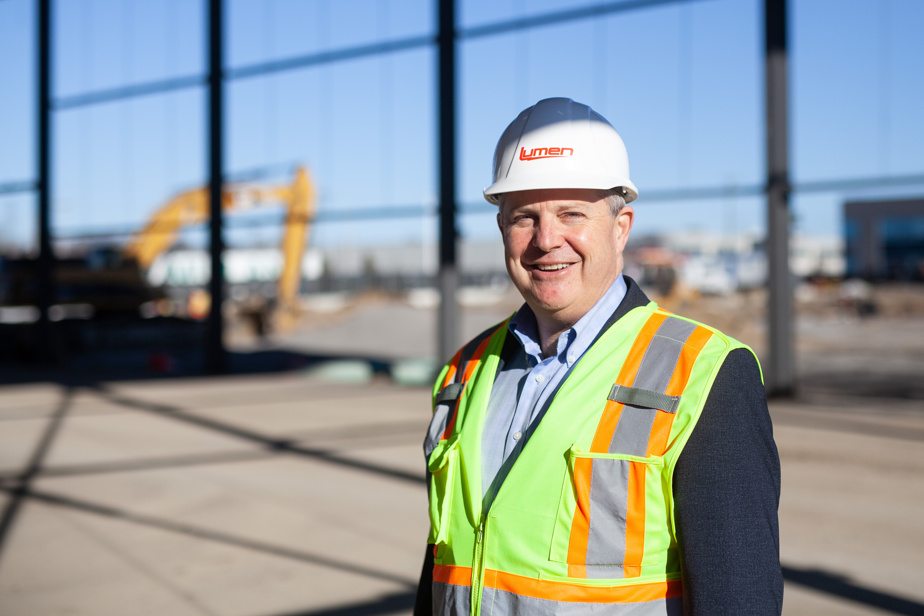
PHOTO KARENE-ISABELLE JEAN-BAPTISTE, COLLABORATION SPÉCIALE
Serge Leblanc, président de Lumen, propriété du Groupe Sonepar
C’est sûr que les personnes aux finances et mon patron me parlent du ratio de fonds de roulement. Mais on a fait un choix à court terme. Oui, je me fais parfois chicaner. C’est leur job de me chicaner et c’est la mienne de prendre la décision appuyée par les propriétaires.
Serge Leblanc, président de Lumen, propriété du Groupe Sonepar
Président d’une société à capital fermé, M. Leblanc estime qu’il n’aurait pas une aussi grande latitude s’il dirigeait une entreprise cotée en Bourse, exposée aux pressions des investisseurs.
De plus, Lumen table sur une croissance de ses activités au cours des prochaines années. L’espace qui sera consacré à l’augmentation des stocks accueillera, lorsque la situation sera rentrée dans l’ordre, de l’équipement afin d’accroître la production.
Ce ne sont pas toutes les entreprises qui sont dans cette situation, souligne M. Leblanc. « Il y a une montée des stocks pour atténuer les problèmes de délais dans la chaîne d’approvisionnement, observe M. Stien, chez GCL Group. Mais tout le monde a commencé à commander de plus en plus, ce qui accroît la problématique dans la chaîne. »
À changer
Selon la PDG de Manufacturiers et Exportateurs du Québec (MEQ), Véronique Proulx, « il n’y a pas un responsable dans le secteur manufacturier qui n’est pas en train de revoir sa stratégie » d’approvisionnement.
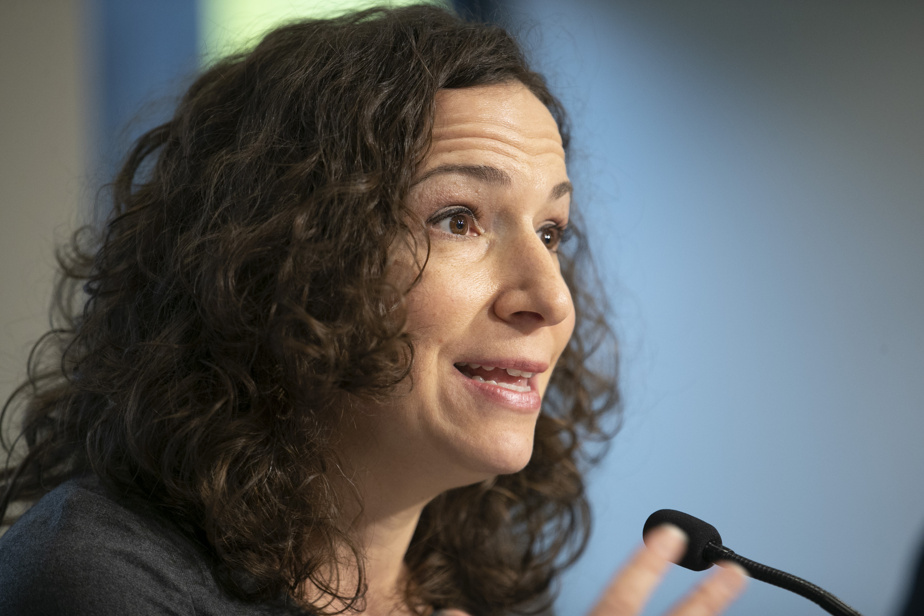
PHOTO DAVID BOILY, ARCHIVES LA PRESSE
Véronique Proulx, PDG de MEQ
C’est un modèle qui ne tenait pas compte de la variable pandémie. Maintenant, c’est là pour de bon et c’est sûr qu’elle vient changer le modèle et l’écosystème.
Véronique Proulx, PDG de MEQ
Malgré l’efficacité du modèle juste-à-temps, des failles avaient déjà commencé à apparaître il y a environ trois ans, souligne M. Stien. Avant l’arrivée de la COVID-19, les chaînes d’approvisionnement étaient bien rodées, rappelle l’expert. Un imprévu, comme une grève au port de Los Angeles, l’une des portes d’entrée des conteneurs en provenance de l’Asie, était suffisant pour provoquer des perturbations, note-t-il.
Chez nous, les grèves des débardeurs au port de Montréal ainsi que des cheminots de la Compagnie des chemins de fer nationaux du Canada (CN) à l’automne 2020 avaient aussi rapidement provoqué des turbulences.
Le juste-à-temps
Avantages
- Stocks réduits, donc moins d’investissement
- Flexibilité pour répondre aux demandes des clients
- Moins d’espace nécessaire pour l’entreposage des produits
Désavantages
- Dépendance accrue vis-à-vis des fournisseurs
- Planification plus complexe
- Vulnérabilités à l’égard de la chaîne logistique
Un équilibre encore difficile à trouver
Relocalisation de la production, diversification des fournisseurs, plans de contingence et stocks plus garnis : il existe des moyens pour atténuer les risques du modèle juste-à-temps. Le défi consiste à trouver l’équilibre entre l’efficacité et la résilience.
Professeure agrégée au département de gestion des opérations et de la logistique de HEC Montréal, Marie-Ève Rancourt croit que la pandémie a fait réaliser aux entreprises l’importance d’avoir des plans de contingence.
Il est toutefois difficile de savoir si toutes les anciennes habitudes seront réévaluées.
Est-ce que je vais avoir quatre fois plus de stock au cas où il y a un tremblement de terre ou une pandémie ? Avoir un fournisseur au lieu d’en avoir quatre, c’est moins cher. Faites-vous quatre épiceries ?
Marie-Ève Rancourt, professeure à HEC Montréal
Des géants comme Intel et Apple ont délié les cordons de leur bourse pour rapatrier la fabrication de certaines pièces aux États-Unis. Dans le cas d’Intel, il s’agit de production de semi-conducteurs. Toutefois, les entreprises qui ont les reins assez solides pour prendre ce genre de décision ne courent pas les rues. « C’est très coûteux et aujourd’hui, on n’a pas la main-d’œuvre pour ramener tout cela en Amérique du Nord, souligne Simon Stien, chez GCL Group. Il faut aussi grandement miser sur l’automatisation. »
De l’avis de la PDG de Manufacturiers et Exportateurs du Quévec (MEQ), Véronique Proulx, il n’y a « pas de modèle unique » à adopter dans le contexte actuel. Certains vont opter pour l’emmagasinage, tandis que ceux qui s’approvisionnent essentiellement en Asie vont peut-être tenter de trouver des fournisseurs situés plus près géographiquement, affirme-t-elle.
Pour ceux qui vont continuer à miser sur l’Asie, le [juste-à-temps] pourrait être plus difficile à maintenir.
Véronique Proulx, PDG de MEQ
Des initiatives ont déjà été déployées pour tenter de rapatrier une partie de la production. Aux États-Unis, le plan d’infrastructures de 2000 milliards US du président Joe Biden prévoit une enveloppe de 300 milliards pour épauler le secteur manufacturier américain.
Au Québec, le gouvernement Legault a déjà exprimé à plus d’une reprise sa volonté de voir les entreprises fabriquer davantage dans la province.